How is AI Used in Manufacturing?
Oftentimes, you’ll need to implement AI technology from multiple categories mentioned above to maximize efficiency. 3D printing could also completely transform housing development by automating the design and construction processes, dramatically lowering costs and increasing access. Whether predicting electrical outages, optimizing resource use, or minimizing downtime in refineries, energy companies are using AI to accelerate key workflows that save time and money. Manufacturing organizations everywhere use our AI solutions to gain valuable insights from the large amounts of data they generate. Here are a few key industries where you’ll find NetApp customers reaping big AI rewards. Productivity and efficiency will be rocketed to new heights, processes will be smoother and the future possibilities are endless.
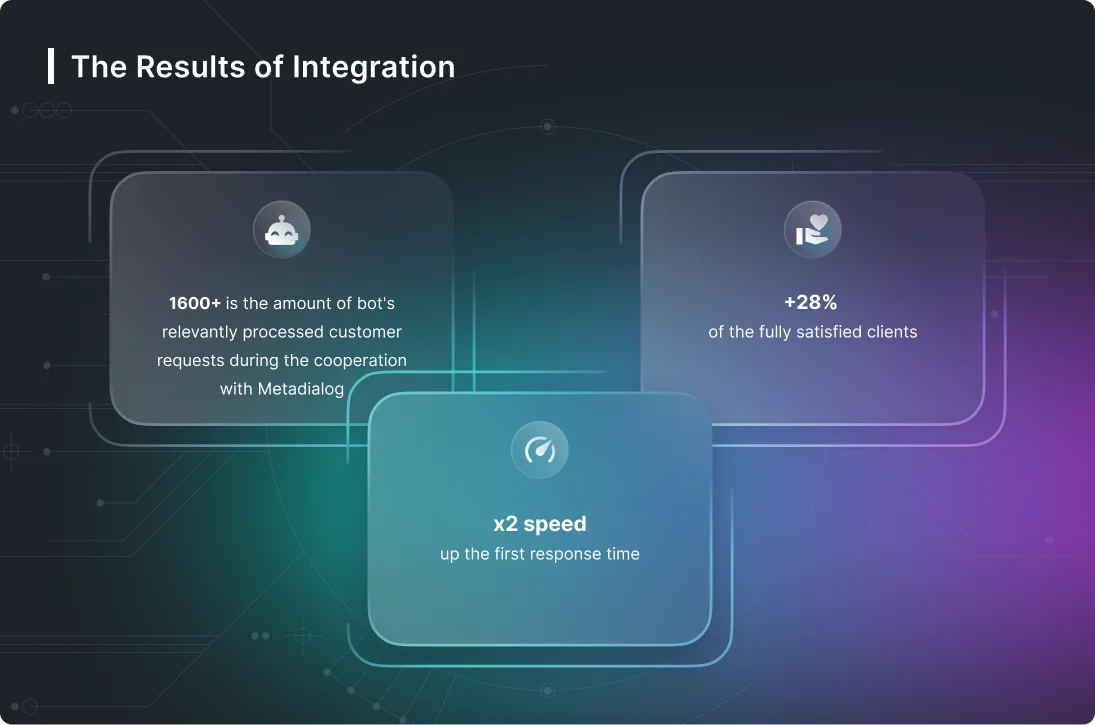
A smart component can notify a manufacturer that it has reached the end of its life or is due for inspection. Rather than monitoring these data points externally, the part itself will check in occasionally with AI systems to report normal status until conditions go sideways, when the part will start demanding attention. This approach cuts down on the volume of data traffic within the system, which at scale can become a significant drag on analytic processing performance. Design, process improvement, reducing the wear on machines, and optimizing energy consumption are all areas AI will be applied in manufacturing. Generative design can create an optimal design and specifications in software, then distribute that design to multiple facilities with compatible tooling.
The Future of Artificial Intelligence in Manufacturing
Those are just a few of the many issues plaguing the manufacturing industry. But thanks to a combination of human know-how and artificial intelligence, data-driven technology — better known as Industry 4.0 — is transforming the entire sector. Deep learning is still small but gaining significant momentum in the process industries. Process manufacturing factories produce massive amounts of data and frequently encounter complex analytical issues, making deep learning a valued tool for manufacturing companies.
Autonomous robots or robotic process automation equipped with AI can perform a variety of tasks in manufacturing companies, such as assembly, material handling, and quality assurance. This technology helps manufacturers improve efficiency, reduce costs, and improve worker safety. AI-driven predictive analytics uses historical data, market trends, and external factors to forecast demand accurately. This is crucial for manufacturers to adjust production levels, resource allocation, and inventory management.
AI as a Supportive Tool for Workers
You can go a step further, taking advantage of the power of predictive maintenance and estimating the probability of the machinery failure (with regression approach) or even its time (with classification approach). Once it occurs, the manufacturing capacities of the factory shrink or even drop to zero, causing financial damage. Even the shortest production stoppage may result in lowered quality, making the first batch of the product unsuitable for the market. To improve the current repeatable batch production processes, a producer of pharmaceuticals approached us to implement AI models and utilize predictive modeling. AI has enabled rapid progress of manufacturing in recent decades, making the factories less labor-dependent and more efficient than ever. The introduction of machine learning was a milestone for this sector – the machinery, until then entirely dependent on the programming, would now be able to make its own decisions based on data.
These include a lack of training data, poor quality images/videos, as well as initial setup costs. For instance, FIH Mobile are using it in smartphone manufacturing to highlight defects. We’ll also be highlighting a number of current AI use cases in manufacturing, and describing how companies use training data platforms (such as V7) to train and deploy AI models. In a world dominated by artificial intelligence, data, and ever-advancing connectivity technologies, it’s the ‘Internet of Things’ out of a list of innovative and game changing technologies. In the video below, you can learn more about MobiDev’s approach to AI-based visual inspection system development. With that said and done, let’s move on to talk about the many applications of artificial intelligence in the manufacturing industry.
The Confluence of AI and Manufacturing
With the pandemic, many manufacturers have started noticing that such a planning model will not take them far in the long run. Even during a relatively stabilized period, the demand for the products can fluctuate, and the planning systems should take these changes into account. Modern APS systems fuelled by artificial intelligence update the production plan based on real-time data, reacting to these changes on an ongoing basis. Today, the applications of AI in manufacturing are numerous – from advanced predictions through quality assurance to waste reduction.
Switch failure comprises the biggest category of failure causes and solving this problem would greatly improve the overall network and infrastructure performance. According to Strukton Rail, predictive maintenance as a solution to this problem leads to higher rail availability at lower costs. It also minimizes unplanned downtime of machinery, reduces maintenance costs, and extends the lifespan of machinery. AI is the perfect fit for a sector like manufacturing, which produces a lot of data from IoT and smart factories.
How Artificial Intelligence is Revolutionizing Social Media to Drive Higher Engagement
Some of the primary benefits of AI in manufacturing include more effective maintenance, improved decision-making and, ultimately, more uptime. With equipment running at full capacity more often, production throughput will naturally increase, yielding higher output and better quality. All of this is important because data has shown that predictive maintenance tools are reducing downtime by as much as 50%, while at the same time boosting machine life by up to 40%. Not just that, but such solutions let managers monitor the current machine status of all their systems. By tracking data in real time like this, they can imitate real-time responses, as well as quickly understand the forecasted state of damage. Ultimately, improving product assembly processes via computer vision lowers the cost of production in the manufacturing industry by completing assembly processes with less error.
Robotic processing automation is all about automating tasks for software, not hardware. It applies the principles of assembly line robots to software applications such as data extraction, form completion, file migration and processing, and more. Although these tasks play less overt roles in manufacturing, they still play a significant role in inventory management and other business tasks. This is even more important if the products you are producing require software installations on each unit. For all of the technologies that we’ll discuss that have applications in manufacturing industries, artificial intelligence is not the most accurate way to describe them.
AI in Business: Impact, Benefits, and Applications
Moreover, AI applications in manufacturing can optimize energy consumption, minimize waste, and improve sustainability efforts. AI-powered systems can analyze energy usage patterns, identify areas of inefficiency, and recommend energy-saving measures. This not only reduces environmental impact but also leads to cost savings for manufacturers. Foxconn, manufacturing electronic products for such giants as Apple, Nintendo, Nokia, Sony, and others, successfully adopted Google Cloud Visual Inspection AI for quality control in its factories. This machine learning program launched by Google in 2021 helps manufacturers inspect product defects, and, eventually, decrease costs of QA.
- This entails using AI-based, data-driven models for customized manufacturing decisions, predictions, and real-time optimization, thereby transforming the manufacturing landscape.
- These insights help streamline processes and identify bottlenecks so that manufacturers can take action.
- Still, more importantly, every process needs to be auditable – and that will also necessitate human involvement.
- After the assembly line, all finished components make their way to the test line, as it’s known, where they are put through their paces — or, we might say, through their angles, windings, and function.
They are needed to help companies process and organize the big data, turn it into actionable insight and write the AI algorithm to perform the necessary tasks. There is abundance of data we generate in the manufacturing process and it is important we aggregate, catalog and use the data to solve the business problem. It is also important that we have a strategy on how we store and use data in the physical and logical perspective. Our governing principle in driving Industry 4.0 or smart factory initiatives is that, “If we are able to digitalize it, then we can visualize it.” After we can visualize it, we can optimize it. Explore the latest industrial maintenance best practices, trends and news from ATS and learn from industry experts and leading manufacturers. Companies are already leveraging it to speed up their processes, improve safety, assist manual workers so that their skills can be used better elsewhere, and ultimately improve their bottom line.
Read more about https://www.metadialog.com/ here.